Energy Efficiency
Increase Energy Savings With Compressors For Manufacturing
Energy efficiency has been a rising trend in North America due to the increasing energy costs and the environmental concerns caused by greenhouse gas emissions.
In numerous industrial plants, the compressed air system is one of the largest energy consumers, accounting for as much as 40% of the total electricity bill.
The energy cost represents as much as 70% of the total lifecycle cost (LCC) of the compressor. That is why improving the energy efficiency of a compressed air installation can save a lot of money for your company.
How Are You Able To Save Energy?
Air Audit
Energy audits of your compressor room are incredibly useful tools that help determine whether your existing air system is as efficient and reliable as possible. With energy costs making up the largest share of a compressed air system’s costs, such a compressed audit may save companies a lot of money.
What is a Compressed Air Assessment?
The main purpose of a compressed air assessment is to gain a full understanding of the energy used by the compressed air system, as well as to suggest small, quick adjustments that you can make to maximize efficiency. These assessments will often uncover issues and it can be a great place to start if you have a small facility with a limited budget.
What is a Compressed Air Audit? A full-scale compressed air audit is a much more thorough, in-depth look at your compressor system. Air audits typically utilize data loggers to measure power (kW), pressure, flow, dewpoint, temperatures, etc., and are designed to provide a very detailed look at the compressed air utilization within a given system. To gather needed information, data loggers are attached to the air compressors and throughout the compressed air network for a minimum of 7-14 days to observe and record system dynamics throughout the normal work week.
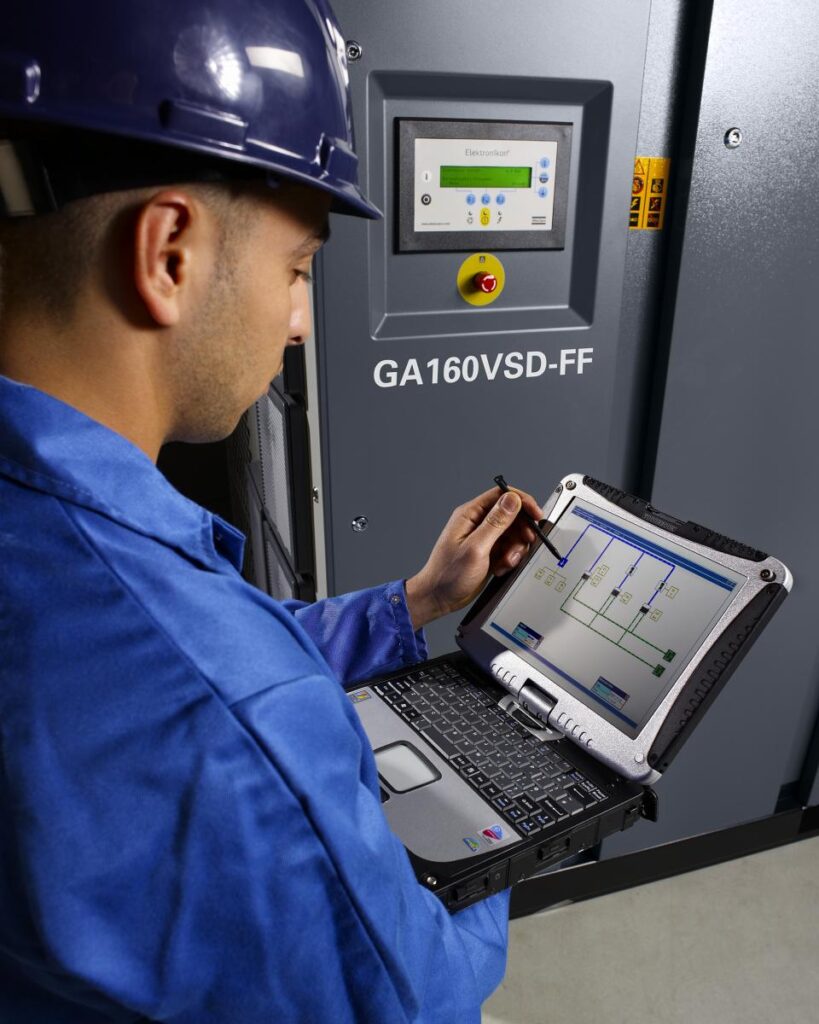
Do I Need an Air Assessment or an Air Audit?
Cost is the biggest differentiator between the two. An in-depth audit will have a higher associated cost depending on what is covered. Audits also take longer to complete depending on the size of the facility and the desired outcome. Not every facility needs to do a full compressed air audit, as sometimes a simple walk-the-line assessment can satisfy the needs and result in substantial energy savings.
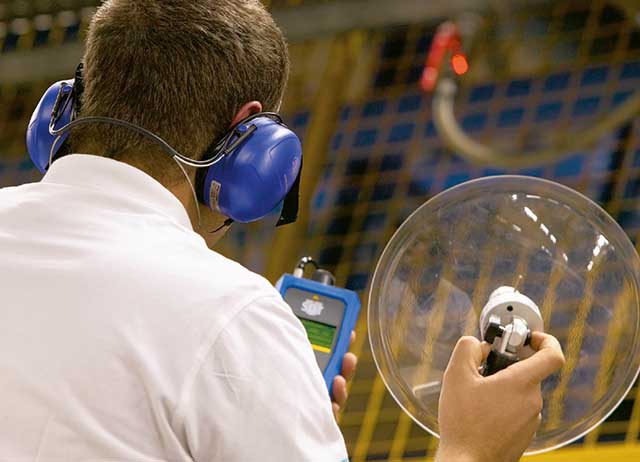
Reduce Unloaded Operating Hours
Air demand in an industrial compressed air system typically fluctuates. If left running after hours or unevaluated, they can use as much as 25% of full load energy in part-load condition. Lower periods of production can be some of the most inefficient times of operation for the air compressors as they are oversized for these periods.
Air leaks
In our experience, older compressed air systems leak between 10% – 50% of the total compressed air consumption. Air compressors are the largest energy consumers in the typical manufacturing plant. In our experience, older compressed air systems leak between 10% – 50% of the total compressed air consumption. Any reductions in demand on the compressed air system can result in real savings to the bottom line. Compressed air leaks are a prime opportunity for low-hanging fruit when looking to reduce compressed air demand. Compressed air is one of the most expensive “utilities” in your plant and is often the most overlooked regarding potential energy savings.
Common Sources of Leaks and Inefficient Air Uses
The first question to ask is how much a can a leak cost. The next question is how to identify a leak and where to look for common sources of compressed air leaks.
Some of the most common leaks and inefficient/unproductive uses of compressed air can be found in the list below:
- Air hoses and air hose connections
- Open blow-offs
- Worn disconnects
- Leaking or failed drains
- Failed seals, O-rings, or gaskets
- Inappropriate air uses such as air brooms or as personal air cooling
- Unused process equipment
- Using compressed air to cool cabinets such as control or electric panels
Now that we have identified some usual sources of air leaks and inappropriate uses of compressed air, we can look at some ways to reduce your overall inefficient uses of compressed air.
If your compressed air system has not been audited recently, you could be missing out. System efficiency, injury prevention, and reliability are just three reasons why regular audits from a manufacturer or certified distributor are essential.
Reduce the pressure band
Reducing the pressure effectively decreases energy consumption. For every 5psi decrease in pressure, energy consumption is lowered by upwards of 3%. Decreasing air pressure also reduces the influence of leaks as the rate is lessened by the lower pressure.
Energy Recovery
Nearly 50% of all industrial processes include the usage of hot water or steam. Energy recovery units can cut back both fuel and maintenance costs of alternative equipment. The by-product of air compressor heat accounts for almost 90% of the energy that is required by the machine. Our heat recovery systems can utilize the heat in the compressor oil through plate exchangers to heat water for any process.
Upgrade to new technology
Installing a new VSD compressor is a guaranteed path to energy savings.
Upgrading your old compressor with the Atlas Copco controller will enable you to take advantage of the most advanced scheduling management.
Contact the Compressors For Manufacturing team to discuss energy recovery in your facility